Quality assurance and quality control are essential processes across countless industries to ensure goods and products meet the standards put in place by the developing company. From testing the pH levels in personal hygiene products during manufacturing to verifying temperature consistency in packaged food items, quality control ensures the well-being and satisfaction of the end user. When it comes to the creation of medical devices, quality control is exceedingly crucial. Dynamic Group Inc., a trusted provider of the most critical components to the world's leading medical device manufacturers, plays a significant role in this process. In this article, we will explore the significance of quality assurance and quality control measures, specifically during the injection molding process of medical device manufacturing.
The Importance of Quality Control in Medical Device Manufacturing
Even though they may seem interchangeable, quality control and quality assurance actually play different roles. Quality control is all about the product, while quality assurance focuses on the process. Both are key to making sure the final product meets the specific standards. Quality assurance occurs before and during manufacturing, while quality control occurs during and after.
Quality assurance (QA) and quality control (QC) matter for all types of goods and products. However, it is particularly impactful when it comes to manufacturing medical devices. These devices and components are not just products, they are often used in life-saving measures. They must be dependable and reliable, which is why quality assurance before and throughout the manufacturing process, as well as quality control afterward, is so important.
Related Article: How Prototype Injection Molding Reduces Production Risks
As described in an article from Qualizeal, one of the main reasons why quality assurance and quality control are essential in medical device manufacturing and testing is the risks that come with faulty devices. Inadequately tested or poorly designed medical devices can lead to significant health risks for patients. According to a report by ECRI Institute, a nonprofit organization that focuses on patient safety, “medical device failures resulted in over 1,900 injuries and 83 deaths in a single year in the United States alone.”
Additionally, the cost of medical device recalls due to quality issues can be staggering. “In 2019, the FDA issued 87 medical device recalls, affecting over 21 million units.” These recalls can result in financial losses and harm to a company's reputation.
In light of this, quality assurance is vital in medical device testing to ensure that devices are both safe and effective for patient use. Quality assurance and quality control processes is the solution that helps manufacturers minimize risks, decrease the chances of recalls, and enhance patient outcomes.
Source: Why is Quality Assurance Important in Medical Device Testing? - QualiZeal.
https://qualizeal.com/why-is-quality-assurance-important-in-medical-device-testing/
Stages of Quality Assurance in Injection Molding
Material Selection and Pre-Production Testing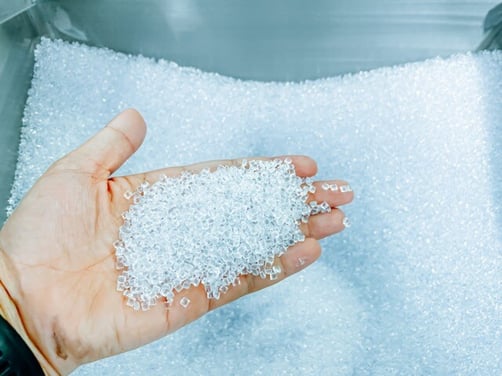
Once a design is approved and the injection molding process begins, one of the first steps is material selection. Material selection is critical because different metals and plastic types must be carefully chosen to ensure the best suitability for the specific device. Then, before injection molding and production begins, pre-production testing is performed to verify that the chosen materials meet all required standards for strength, biocompatibility, and performance.
Additionally, when it comes to medical components and devices, compliance with industry regulations, such as FDA guidelines and ISO 13485, must be met.
In-Process Monitoring for Precision Molding
Quality assurance techniques and real-time monitoring are used throughout the injection molding process. Some of the methods of doing this include:
- Temperature control
- Flow rate monitoring
- Viscosity measurement
- Mold cavity pressure sensing
- Cycle time tracking
- Part weight measurement
Post-Molding Quality Control Checks to Identify Defects and Ensure Compliance
After the injection molding process is complete, quality control inspection takes place to ensure the product meets standards and is compliant. This can include methods such as:
- Visual checks
- Dimensional analysis
- Functionality testing
- Material testing
- Biocompatibility testing
These rigorous quality control practices contribute to reliable and safe medical devices. Quality control and assurance not only help to ensure that molded medical components and devices meet quality and safety standards, but it also contributes to a company's reputation.
Choosing the Ideal Precision Molding Partner for Your Medical Devices
The ongoing innovation in quality assurance, quality control and injection molding production methods is crucial to keeping pace with the increasing demands of the industry. At Dynamic Group, we prioritize continuous improvement and innovation to ensure that we stay at the forefront of delivering high-quality medical solutions.
Contact us today to discuss your next tooling or molding project.
Dynamic Group is a trusted provider of the most critical components to the world's leading medical device manufacturers. As leaders in innovative design solutions for complex Plastic and MIM molds, our extensive molding and tooling capabilities allow us to operate as a reliable, high-performing extension of your organization. Focusing on creating world-class value for our partners, we cultivate relationships to ensure successful product launches within budget.
Request a quote today and take the first step in your next design. Our expert team is here to provide tailored solutions that meet your specific needs.
November 18, 2024